Process Metallurgy group
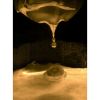
Fall of molten drops in a liquid metal bath (maraging steel), observed with a HD video camera in the electron beam melting device
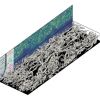
Numerical simulation of a turbulent boundary layer with turbulence forcing in the external flow
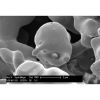
Metallic iron grains obtained after direct reduction of the ore by H2
Last publications
- Exposure of fractal aggregates to accelerating flows at finite Reynolds numbers
Akash Saxena, Jean-Sébastien Kroll-Rabotin, R. Sean Sanders
International Journal of Multiphase Flow, 2025, 182, pp.105018. ⟨10.1016/j.ijmultiphaseflow.2024.105018⟩ - Study of Assimilation of Cored Wire into Liquid Steel Baths
Edgar-Ivan Castro-Cedeno, Julien Jourdan, Jonathan Martens, Jean-Pierre Bellot, Alain Jardy
Metals, 2024, 14 (4), pp.462. ⟨10.3390/met14040462⟩ - Primary and secondary breakup of molten Ti64 in an EIGA atomizer for metal powder production
Baraa Qaddah, Pierre Chapelle, Jean-Pierre Bellot, Julien Jourdan, Gagan Kewalramani, Agathe Deborde, Raphael Hammes, Nicolas Rimbert
Powder Technology, 2024, 438, pp.119665. ⟨10.1016/j.powtec.2024.119665⟩
Presentation
The group is specialized in the field of metallic materials process engineering, a novel thematic attempt to bring the “process engineering” scientific approach into the academic and industrial “materials” community. It requires various skills in domains such as thermodynamics, transport phenomena, continuum mechanics and numerical techniques. A key point in all research works is the theoretical or/and experimental study of coupled transfers (fluid flow, heat and mass transfer, etc.)
An important activity is the mathematical modelling and numerical simulation of pyrometallurgical processes. Thanks to the continuous improvement in numerical methods, the research in this area has considerably developed, and provides new effective scientific tools, such as multiscale and multi-physics software.
Nevertheless, the experimental part is in no way neglected, as it is required for:
- characterization of the physical and chemical mechanisms involved during the processing and treatment of metallic materials
- validation of the numerical models by means of laboratory scale measurements, as well as experiments achieved on pilot plants when available, and full-scale production units.
Experiments on actual “full scale” production plants represent an original approach in which the group has gained a strong experience.
Almost all studies are performed in tight collaboration with the process users in the industry, mostly in the frame of PhD works.
The research group also hosts the Industrial Chair “Liquid Metal Processing”, launched in 2019 at the Université de Lorraine and funded by local institutions as well as an industrial consortium composed of 5 companies: ArcelorMittal, Aperam, Eramet-A&D, Safran and Vallourec.
Research topics
Melting and remelting processes
For around 30 years, the group has been known as an international academic leader in the field of melting and remelting of various metallic alloys (titanium, zirconium, maraging steel, Ni-based superalloys), in particular in modelling of refining processes to help optimization of the units. Vacuum arc remelting (VAR), electro-slag refining (ESR), electron beam melting (EBM), vacuum arc skull melting (VASM), and plasma arc melting with cold hearth refining (PAM-CHR) have been the object of many PhD studies in collaboration with the industry (Eramet, Safran, Timet Savoie, Framatome and Aperam).
Permanent staff:
Alain Jardy, Jean-Pierre Bellot, Pierre Chapelle, Thibault Quatravaux
Conferences:
Liquid Metal Processing and Casting LMPC, every 2 years, alternatively in Europe and the US.
Thesis:
Running in 2020, 5 PhDs under CIFRE conventions with industrial partners and 1 post-doc internship, Léa Décultot, Rayan Bhar, Jérémy Chaulet, Jérémie Haag, Thomas Poullain, Julien Banos
Articles:
- On the modelling of thermal radiation at the top surface of a vacuum arc remelting ingot, Delzant et al., Met. Trans. B 2018, 49, 958-968
- A 2D multiphase model of drop behavior during Electroslag Remelting, Chaulet et al., Metals 2020, 10, 490
Reduction of CO2 emissions from the steelmaking industry
Nowadays, steelmaking is directly responsible for about 7% of the anthropogenic greenhouse effect in the world. The group investigates various alternatives to the conventional processing route based on blast furnaces and oxygen steelmaking, such as:
- the so-called direct reduction of the iron ore by an H2-CO syngas, to halve CO2 emission;
- the direct reduction of ore by pure H2, which could reduce CO2 emission by 80%;
- a completely new process, the reduction by biomass in a shaft furnace, combined with recycling.
Permanent staff:
Fabrice Patisson, Olivier Mirgaux
Project:
PIA Valorco, 2014-2019
Thesis:
Labex DAMAS 2019-2022, Tao WANG
Articles:
- Detailed modeling of the direct reduction of iron ore in a shaft furnace, Hamadeh et al., Materials 2018, 11, 1865
- Carbon impact mitigation of the iron ore direct reduction process through computer-aided optimization and design changes, Béchara et al., Metals 2020, 10, 367
Inclusion behavior in liquid metals
In metallurgical reactors, such as liquid steel treatment ladles or aluminum refining units, physical and chemical reactions lead to an evolution of the inclusion population which is responsible for the cleanness of the final product. CFD simulations at full process scale are combined with local approaches to improve the understanding of interactions at smaller scale: aggregation, deposition, and capture at interfaces.
Permanent staff:
Jean-Pierre Bellot, Jean-Sébastien Kroll-Rabotin, Thibault Quatravaux
Project:
ANR-DFG Flotinc 2016-2019
Thesis:
- CIFRE Affival 2016-2019, Edgar CASTRO CEDENO
- ANR Flotinc 2016-2019, Mathieu GISSELBRECHT
- LabEx DAMAS 2016-2019, Manoj JOISHI
Articles:
- Toward better control of inclusion cleanliness in a gas stirred ladle using multiscale numerical modeling, Bellot et al., Materials 2018, 11, 1179
- Numerical simulation of modification of non-metallic inclusions by calcium treatment in the argon-stirred ladle, Castro et al., Met. Res. Tech. 2019, 116
Environmental issues
In order to either reduce the impact of existing processes for the fabrication and treatment of materials on the environment or design new processes, a rigorous approach is required to evaluate the impact. The group has developed an original methodology which associates process systemic modelling and Life Cycle Analysis (LCA) of products, processes, and routes. In this approach, the use of systemic modelling ensures a high quality of the life cycle inventory.
Some recent applications:
- a comparison of biomass-based heat and electricity co-generation processes in terms of energy and environmental impacts;
- the evaluation of several processes for the capture of CO2 originating from a coal-fired plant.
Permanent staff:
Olivier Mirgaux, Fabrice Patisson
Project :
Pacte Lorraine CTSA, 2016-2019
Thesis:
CNRS-Région Grand Est 2016-2019, Hélène ANSELMI
Articles:
- From trees to electricity, the physics beyond the LCA, Mirgaux et al., Matériaux et Techniques 2016, 104-106, 1179
- Simulation of post-combustion CO2 capture, a comparison among absorption, adsorption and membranes, Anselmi et al., Chem. Eng. Technol. 2019, 42, 797-804
Vacuum electric arcs
These studies aim at better understanding the phenomena involved in the behavior of electric arcs between metallic electrodes, operating under vacuum, in order to help controlling the devices where such arcs are present. Based on both experiments and numerical simulation, researches are devoted to the characterization of arc regimes, to the analysis of the arc dynamics, and to the modelling of the plasma jets and of arc-electrode interactions. A key feature is the observation and measurement on industrial units.
Permanent staff:
Pierre Chapelle, Alain Jardy
Thesis:
- CIFRE Timet Savoie 2015-2018, Pierre-Olivier DELZANT
- Supergrid Institute 2015-2018, Benoît TEZENAS DU MONTCEL
Articles:
- Numerical study of the current constriction in a vacuum arc at large contact gap, Tezenas du Montcel et al., IEEE Trans. Plasma Sci. 2019, 47, 2765-2774
- Investigation of arc dynamics during vacuum arc remelting of a Ti64 alloy using a photodiode based instrumentation, Delzant et al., Jl. Mat. Proc. Tech. 2019, 266, 10-18
Know-how
Mathematical modelling and numerical simulation
- In-house built software dedicated to process simulation (Solar, Reductor, Flua, DissolFil, etc.)
- Finite volume method for the solution of liquid or gas flows and coupled transfers
- Lattice-Boltzmann and immersed boundary methods for the modelling of inclusion behavior
- Developments on commercial or open-source software – Ansys Fluent, Comsol, OpenFoam, Aspen Plus, GaBi, Factsage
Liquid metal processing
- Vacuum Induction Melting 50 kW furnace fully equipped for the melting of metals and alloys up to 1650 °C. Possible use of a graphite susceptor
- Cold Crucible Induction device (200 kW) for the melting of reactive metals (Ti, Zr) or the liquid treatment avoiding contact with a refractory crucible
- Laboratory-scale Electron Beam Melting furnace (1 EB gun, maximal power 100 kW) operating under high vacuum (10-5 - 10-4 mbar) and equipped with a small ingot casting facility, (up to 100 mm in diameter) suitable for drip-melting or cold hearth operation
Gas/solid reactions
- Park of thermobalances for thermogravimetry experiments (from the room temperature up to 2400 °C) under inert or reactive gases such as H2, CO2, CO, H2O
- Differential Thermal Analysis
Physical and chemical characterization
- Gas chromatography
- Mass spectrometry
- Fourier Transformation Infra-Red (FTIR) absorption spectroscopy
- Carbon/Sulphur analysis in solid compounds (from 1 ppm to 100%)
- Glow discharge optical spectroscopy
- Sieverts’ technique
- High definition and high speed videocamera
- Infrared thermography
Technology transfer
- In 2018, creation - by a former post-doctoral fellow - of the start-up O2M Solutions, specialized in high performance computing, process simulation and OpenFOAM®
Members
CNRS researchers
- Pierre CHAPELLE
Professors, assistant professors
- Jean-Pierre BELLOT
- Jean-Sébastien KROLL-RABOTIN
- Olivier MIRGAUX
Tenure tracks
- Thibault QUATRAVAUX
- Isnaldi RODRIGUES DE SOUZA FILHO
Technical and support staff
- Julien JOURDAN
- Jean-Baptiste LETZ
PhD students
- Hamid BELLACHE
- Rabeb BEN HASSINE
- Devtanu BOSE
- Soraya DOUMANDJI
- Ifzal HUSSAIN
- Ashutosh KUMAR
- Antoine MARSIGNY
- Mariana MAYER GRIGOLETO
Emeritus
- Fabrice PATISSON
Publications
Contact
Head of the group
Thibault QUATRAVAUX
thibault.quatravaux@univ-lorraine.fr
+33 (0) 3 72 74 29 00
Nancy-Artem
Institut Jean Lamour
Campus Artem
2 allée André Guinier - BP 50840
54011 NANCY Cedex