STRATO-CONNECT (Study of conductivity and adhesion conditions of metallic deposits by spraying on interstrates)
The Stratoconception Additive Manufacturing (AM) process enables the solid layered fabrication of 3D objects of complex exterior and interior shapes in a wide variety of materials. The objective of incorporating sensors within the internal structure of objects was already to provide precise information on the environment of the object but also on its behavior during its life cycle. This acquired information will then make it possible to control and adapt the behavior of the 3D object and / or modify its environment. This control is carried out by monitoring software equipped with decision algorithms reacting in real time to the information transmitted by the on-board sensors. The management of the very large volumes of acquired data then allows an evolutionary and adaptive learning of the objects.
Currently, the work carried out by CIRTES relates to the direct integration of miniature discrete components and also to their direct construction. The envisaged technology requires the creation of electrically conductive tracks connecting these elements to each other as well as to the outside. The final objective of our entire approach is to transform a 3D object into a true intrinsic sensor and no longer into a simple object incorporating a sensor. Ultimately, this involves depositing, during AF on a transparent polymeric interstrate, conductive metal tracks by anchoring in the subsurface a stable interlayer of conductive particles by SND (Supercritical Nitrogen Deposition) then a layer more thick deposited by CSD (Cold Spray Deposition). Initial work was carried out with TJFU and CM2T and led to the creation of such 3D conductive tracks.
The work already carried out has made it possible to create functional demonstrators, but improvements in adhesion properties as well as in conductivity remain to be explored and understood. This will mainly involve establishing, through fine local and / or global characterizations, the relationships between the microstructure and the physical and mechanical properties of the composite polymer substrate + Cu deposit system, the reference system initially. In particular, the electrical performance will be studied as a function of the porosity rate of the parts, the mechanical properties such as adhesion and resistance to the removal of deposits will also be determined. Indeed, it would seem that a certain number of physical mechanisms are still not perfectly mastered, which can sometimes generate versatility in the performance targets of the composites produced, although the deposition can be perfectly carried out from a purely technological point of view. The identified industrial applications of this process are multifunctional 3D polymeric objects for the Aeronautics, Automotive, Luxury, etc. sectors.
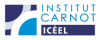