Microstructures and Stresses group
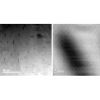
Coherent precipitation of nanometric chromium nitrides during the isothermal decomposition at 600°C of an austenite enriched in carbon and nitrogen from 23MnCrMo5 steel. Images were obtained by High Resolution Transmission Electron Microscopy.
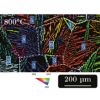
EBSD cartography illustrating the quantification of the microtexture of the α phase by the number of αWGB colonies per grain. The α phase is represented in IPF mode and the phase in black.
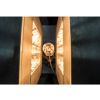
An in-house developed lamp furnace that allows the monitoring of phase transformations and stresses by X-ray diffraction on synchrotron lines (E>80keV) during controlled heat treatment (International Patent). The sample (solid, powder) can rotate continuously at a speed of up to 10 revolutions per second, increasing the volume analysed and allowing the determination of stresses in different directions. Phase transformation kinetics can also be followed by electrical resistivity measurements.
Last publications
- Oxidation Behavior and Integration into High Power Density Thermoelectric Generators of Commercial Half-Heusler Alloys
Soufiane El Oualid, Philippe Masschelein, Lionel Aranda, Ghouti Medjahdi, Benoît Denand, Arthur Wieder, Ilayda Terzi, Przemyslaw Blaschkewitz, Pawel Ziolkowski, Christophe Candolfi, Bertrand Lenoir
ACS Applied Materials & Interfaces, 2025, 17 (28), pp.40773-40787. ⟨10.1021/acsami.5c08992⟩ - Upscaling transformation plasticity using full field fast Fourier transform simulations of polycrystals undergoing phase transformations under applied loads
Shahul Hameed Nambiyankulam Hussain, Daniel Weisz-Patrault, Benoît Appolaire, Sabine Denis, Amico Settefrati
International Journal of Solids and Structures, 2025, 315, pp.113337. ⟨10.1016/j.ijsolstr.2025.113337⟩ - 3D mosaicity of a single-crystal nickel-based superalloy by lab-based diffraction contrast tomography
Alexiane Arnaud, Jun Sun, Florian Bachmann, Vladimir Esin, Henry Proudhon
Scripta Materialia, 2025, 257, pp.116463. ⟨10.1016/j.scriptamat.2024.116463⟩
Presentation
The Microstructures and Stresses group studies the genesis of microstructures by phase transformations in the solid state and internal stresses during thermal, thermomechanical or thermochemical treatments of metallic alloys. Indeed, the relationships between the different elements of the treatment / microstructures / properties chain need to be known to design and to improve these metallic alloys.
The group's activities are aimed at:
- understanding the mechanisms of microstructures formation by phase transformations in the solid state
- establishing the relationships between microstructures and the generation of stresses during phase transformations
- establishing the relationships between microstructures, stresses and properties ( particularly mechanical properties)
The metallic alloys studied are multi-constituent alloys, but we also examine model alloys (pure, binary, ternary metals). The applications targeted concern the lightening of structures (for the aeronautics and automotive industries) via the optimisation of microstructures generated by different processes (forging, stamping, heat treatments, etc.) or recycling.
A specificity of the group is the study of phase transformation kinetics in situ (dilatometry, resistivimetry, Xray Diffraction by synchrotron radiation, microscopy) under thermal/thermomechanical treatments (temperatures up to 1200°C, speeds varying from 0.01°C/s to 200°C/s). Interactions between stresses and phase transformations are studied: internal stresses are associated with transformation deformation tensor – and/or applied external stresses.
The experimental activities are based on joint modelling work at different scales and combining various approaches (Calphad, phase field, mean fields). Most often, microstructural evolution models are associated with micromechanical models, using different techniques such as finite elements to take into account the local mechanical behaviour at the phase scale.
The group also carries out modelling and numerical simulations during heat treatment at the scale of massive parts (residual stresses, deformations), in the presence of thermal and chemical gradients and taking into account thermal - phase transformation - mechanical couplings.
All of this research is carried out with :
- Academic partners: LEM3, CEMES, Institut P’, Mines ParisTech, SIMAP, GPM, ICMCB, ONERA
- Industrial partners: SAFRAN, Arcelor Mittal, Ascometal CREAS, AIRBUS, Vallourec, PSA, Bosch, IRT M2P, etc.
The group is also strongly implicated in the Labex DAMAS (Design of Alloy Metals for low-mAss Structures).
The group is involved in a number of European H2020 projects under the RFCS (Research Fund for Coal and Steel) programme, including:
- IMMAC: Machinability of high-strength steels, terminé à enlever?
- STEELSECO (Design of new economic secondary precipitating steels for fatigue resistance at elevated service temperatures)
- MIPRE (Advanced metallurgical and micromechanical modelling to deploy the microstructural tailoring potential of press hardening)
- DYNAUSTAB (Austenite Stability under Dynamic loading).
The group also participates in ANR projects:
- HighS Ti: obtaining high-strength harmonic microstructures in titanium alloys by powder metallurgy
- ALTITUDE (new high temperature titanium alloy for tomorrow's aeronautic applications)
- ECUME (Interactions between electric currents and microstructural evolutions)
Research topics
Formation of microstructures by solid-state phase transformations in metal alloys
Transformation kinetics are dependent on nucleation conditions (heterogeneous nucleation at grain boundaries, dislocations, interfaces) as well as growth conditions (local equilibrium, para- equilibrium, etc.).
The group’s work aims to investigate the mechanisms involved in diffusive or displacive phase transformations. These are assessed during heating, isothermal holding and cooling (including rapid thermal cycles), in multi-component alloys (steels, titanium alloys, intermetallics, nickel-based…), model alloys and metal matrix composites.
In the case of steels, here are 3 examples of the group’s work:
- The ANR CAPNANO (CArbon Partitioning in NANOstructured ferritic phases: kinetics and microstructures), 2015-2018 . This project aimed to improve understanding of the phase transformation mechanisms and properties of 3rd generation Ultra High Strength steels obtained by Quenching and Partitioning. The steels acquired by this process are considered a future solution to lighten structures in automotive construction due to their high strength and excellent deep-drawing properties. The group’s work on in-situ characterization using a synchrotron line is considered particularly innovative as it explains for the first time how to establish unbiased carbon balances during partitioning. These results have been supported by numerous measurements with a tomographic atomic probe whilst taking into account the internal constraints resulting from phase transformations.
- Work on the interactions between re-crystallisation and phase transformation processes during the annealing of rolled steels is carried out in collaboration with Arcelor Mittal. During this work, the group developed new techniques on synchrotron lines to monitor in situ these different processes simultaneously. This also led to a better understanding of the influence of carbides and their compositional gradients throughout the process, by coupling nanometric scale analyses in transmission electron microscopy and thermokinetics models.
- For several years, the group has been studying the effects of carbon and nitrogen enrichment of austenite on its decomposition during cooling (high-temperature phase formation sequences leading to novel microstructures, bainitic transformation mechanism, micro-textures, etc.). This research provides a better understanding of the ranges of carbonitriding treatments on parts and the metallurgical consequences.
In the case of titanium alloys, the group developed strong expertise over more than 30 years through many studies associating high-performance characterization means (in-situ XRD, TEM) and fine models of microstructure evolution at all scales. Since the 1990s, 13 thesis have been defended.
2 recent projects are emblematic of the group’s work:
- Research into microstructural changes in industrial titanium alloys during ageing. This is carried out with Airbus and is representative of the conditions of use of certain aeronautical parts.
- Research with Safran Landing Systems concerning microstructural developments in industrial titanium alloys during post-forging heat treatments.
In parallel to experimental characterizations, the group models transformation kinetics based on nucleation and growth/dissolution models. The growth/dissolution laws are analysed (abrupt interface model, diffuse interface model) by comparing the measured speeds with experimental data.
Projects:
- European Steelseco Project (2017-2020)
- Labex DAMAS (2020-2023)
- ANR ALTITUDE (2019-2023)
- ANR ECUME (2019-2023)
- Industrial contract with the CTIF (2018-2021)
- RESEM (IRT M2P)(2020-2021)
- Industrial contract with the Welding Institute (2019-2022)
- Ascometal Industrial contract (2018-2021)
- Industrial contract with ACM-ABS (2018-2020)
Thesis:
- Nicolas Maury (CIFRE Airbus)
- Meriem Ben Haj Slama, Marc Moreno (Arcelor Mittal)
- Utku Deniz Ozturk, Morgan Goetz (CIFRE Safran Landing Systems)
- Steve Gaudez (Steelseco)
- Ivan Cazic (CIFRE Welding Institute)
- Cécile Rampelberg (CIFRE Ascometal)
- Hélène Quehen (CIFRE CTIF), Labex Damas / Onera thesis
- Utku Deniz Ozturk, DocMase (UPC Catalogne – UL Nancy), Erasmus Mundus
Articles:
- Isothermal decomposition of carbon and nitrogen-enriched austenite in 23MnCrMo5 steel, Acta Materialia 148 (2018) 363-373, H.P. Van Landeghem, S.D. Catteau, J. Teixeira, J. Dulcy, M. Dehmas, M. Courteaux, A. Redjaïmia, S. H Denis
- Influence of the ageing conditions and the initial microstructure on the precipitation of α phase in Ti-17 alloy, Journal of Alloys and Compounds, 763 (2018) 446-458., N. Maury, B. Denand, M. Dehmas, C. Archambeau-Mirguet, J. Delfosse, E. Aeby-Gautier
- Phase transformations in PuGa 1 at. % alloy: Influence of stress on δ→α’ martensitic transformation at low temperatures, Materialia, 6 (2019) 100304., B. Ravat, F.Lalire, B. Oudot, B. Appolaire, E. Aeby-Gautier, J.Pansiot, F. Delaunay
- Real-time investigation of recovery, recrystallization and austenite transformation during annealing of a cold-rolled steel using high energy X-ray diffraction (HEXRD), Metals, 9, 1 (2019) 8., M. Moreno, J. Teixeira, G. Geandier, J-C. Hell, F. Bonnet, M. Salib, S.Y.P. Allain
- Carbon heterogeneities in austenite during Quenching & Partitioning (Q&P) process revealed by in situ High Energy X-Ray Diffraction (HEXRD) experiments, Scripta Materialia, 181 (2020) 108-114, SYP Allain, S. Gaudez, G. Geandier, F. Danoix, M. Soler, M. Goune
- Instabilities in the periodic arrangement of elastically interacting precipitates in nickel-base superalloys, Acta Materialia 187 (2020) 41-50, M. Degeiter, Y. Le Bouar, B. Appolaire, M. Perrut, A. Finel
- Crystal structure, morphology and formation mechanism of a novel polymorph of lead dioxide, gamma-pbO(2), Journal of Applied Crystallography, 2019, 52, 304-31, Kabbara, H ; Ghanbaja, J ; Redjaimia, A ; Belmonte, T
Relationships atomistic - microstructures in relation with mechanical properties.
At the microstructure scale, the research of the group aims to:
1. Understand and model the mechanical behaviour of 3rd generation duplex AHSS (Advanced High Strength Steel) microstructures at room temperature. This is carried out in collaboration with ArcelorMittal. This new family of steels for automotive construction brings together several metallurgical concepts that have two common characteristics: large fractions of unstable austenite allowing a TRIP (Transformation Induced Plasticity) effect and a nanostructured ferritic matrix.
This aspect is comprised of 2 axes:
- the development of a physics-based behaviour law for the ferritic lath microstructure
- modelling the TRIP effect itself, in particular induced martensitic transformations, and the determination of the effect of these transformations on work hardening.
2. Determine the behaviour laws of alloys during thermomechanical treatments.
Experimental data are obtained on unique thermomechanical testing machines which allow tensile (compression) tests to be carried out under vacuum or in an inert atmosphere. This is done at a temperature range between 20°C and 1100°C with deformation rates ranging from 10-6 s-1 to 1 s-1.
Thus, thermomechanical behaviour laws have been obtained for the different phases of steels (including in their metastability ranges) within the framework of the ANR Optipro-Indux (2011-2015) or more recently within the framework of K. Jeyabalan's IRT M2P thesis for carbon and nitrogen enriched steels.
Characterization and understanding of mechanical behaviour are also essential elements for the design of titanium alloy microstructures.
At the atomic scale, the team recently developed the study of the plasticity of metals by ab initio simulation. For example, it is interested in the behaviour of dislocations under stress as well as the influence of the addition of alloying elements on the properties of centred cubic metals.
Projects:
- European RFCS Steelseco project (2017-2020)
- LUE project (2019-2022)
- Carnot Welding Institute project (2017-2020)
- Arcelor Mittal Industrial contract (2019-2022)
- RFCS MIPRE (2020-2023)
- RFCS DINAUSTAB (2020-2023)
- Industrial Suturex contract (2020-2023)
Thesis:
- S. Gaudez (Steelseco)
- Solenne Collomb, ICEEL CIFRE – Institut de soudure
- Juan Macchi (LUE Thesis)
- Mathias Lamari (Arcelor Mittal CIFRE)
- Félix Royer (Suturex)
Articles:
- Influence of testing mode on the fatigue behavior of < 111 > austenitic grain at the nanometric length scale for TRIP steels, Materials Science and Engineering: A, 2018, 713, 24, 287-293., JJ Roa, I Sapezanskaia, G Fargas, R Kouitat, A. Redjaïmia, A. Mateo,
- Cosserat crystal plasticity with dislocation driven grain boundary migration, Journal of Micromechanics and Molecular Physics. 2018, A Ask, S Forest, B Appolaire, K Ammar
- Microstructure-based behavior law for globular pearlitic steels, Journal of Materials Research and Technology, 8, 3 (2019) 3373-3376., SYP Allain, A Roth, O Bouaziz, E D'Eramo
- Non-glide effects and dislocation core fields in BCC metals, Nature Partner Journals Computational Materials, 5 (2019) 109., A. Kraych, E. Clouet, L. Dezerald, L. Ventelon, F. Willaime, D. Rodney
- Simulating the mechanisms of serrated flow in interstitial alloys with atomic resolution over diffusive timescales, Nature Communications, 11 (2020) 1227., Y. Zhao, L. Dezerald, M. Pozuelo, X. Zhou, J. Marian
- High-Temperature Deformation Behavior of 718Plus: Consideration of γ′ Effects” Materials, Performance and Characterization, (2020), U. Ozturk, J. Calvo, J. M. Cabrera, J. Ghanbaja, A. Redjaïmia
Internal stresses associated with phase transformations at the scale of phase and processes
During solid-state phase transformations, stresses are generated at the phase scale due to transformation deformations. In many cases, the material tends to minimise the stresses by adapting the morphology of the precipitates and their spatial arrangement.
Research has been carried out on this topic using in situ X-ray diffraction on high-energy synchrotron sources: (ESRF, DESY) or neutrons (ILL, HZB).
In certain cases, this makes it possible to characterize the evolution of average stresses in phases. EF micro-mechanical calculations, FFT methods, and mechanically coupled phase field approaches have also been used.
The processes are either heat treatment (quenching, tempering, induction heating, etc.) or thermochemical treatments (carburizing, carbonitriding, etc.). At this scale, the aim is to understand the genesis of internal stresses and deformations in relation to phase transformations. This involves modelling and numerical simulation of coupled thermal, metallurgical, and thermomechanical phenomena and multi-scale approaches as well as their experimental validation (in situ measurements of temperatures, deformations, internal stresses, etc.).
Recent research has made it possible for the first time to determine experimentally the genesis of internal stresses during cooling in carbonitrided specimens with carbon and nitrogen gradients. This has been performed by X-ray diffraction in situ on a synchrotron, and these results have been compared with those of calculations.
Projects:
- IRT M2P projet TTA (Traitements Thermiques Avancés) (2014-2019)
- RESEM Carbonitru (IRT M2P) (2020-2021)
- RESEM IMASQUE (IRT M2P) (2020-2021)
Thesis:
- K. Jeyabalan (IRT M2P)
- Juan Macchi (LUE Thesis)
- Shahul (Arcelor Mittal)
Articles:
- Simulation of coupled temperature, microstructure and internal stresses evolutions during quenching of a beta-metastable titanium alloy, Materials Science Engineering A651 (2016) 615-625., J. Teixeira, B. Denand, E. Aeby-Gautier, S. Denis
- Internal stresses and carbon enrichment in austenite of Quenching and Partitioning steels from high energy X-ray diffraction experiments, MSE A-Structural Materials Properties Microstructure and Processing, 710, 2018, 245-250., SYP Allain, S. Gaudez, G. Geandier, J-C. Hell, M. Gouné, F. Danoix, M. Soler, S. Aoued, A. Poulon-Quintin.
- In situ stress tensor determination during phase transformation of a metal matrix composite by high-energy X-ray diffraction, Materials, 11(08), 2018, 1415., G. Geandier, L. Vautrot, B. Denand, S. Denis
- Modeling of the austenite decomposition kinetics in a low-alloyed steel enriched in carbon and nitrogen, Materialia 9, 2020, 100582K. Jeyabalan, S.D. Catteau, J. Teixeira, G. Geandier, B.Denand, J. Dulcy, S. Denis, G. Michel, M. Courteaux
Know-how
Devices for monitoring phase transformations in situ
- Dilatometry and resistivimetry to monitor phase transformations in situ during thermal cycles
- Dilatometry (extensometry) and resistivimetry to monitor phase transformations in situ during thermomechanical tests (traction/compression)
- Transportable furnace for large instruments (synchrotrons, neutron reactor etc.), to determine the kinetics of phase transformations by X-ray diffraction and resistivimetry as well as the determination of internal stresses
- Confocal microscopy with heating plate: microstructural evolution during heat treatment
- Heat treatment devices (tilting primary vacuum furnace, controlled atmosphere transfer furnace, vacuum quenching furnace) enable to modify the microstructures of the alloys and generate residual stresses in massive specimen
- Skills in optical, scanning electron and transmission microscopy allow the study of microstructures of alloys. Chemical (EDX, EDS) and crystallographic (EBSD) analyses can be carried out
- Skills in X-ray diffraction (phase fraction, crystallography, stresses)
- Development within the group of expertise through the use of large instruments, high energy XRD (ESRF, DESY, SPRING8), neutron reactor (ILL). Quantitative in situ large set of data on the kinetics of phase transformations and internal stresses are obtained during a heat / thermomechanical treatment
Modelling
- Atomic scale modelling : VASP (ab initio), LAMMPS (molecular dynamics)
- Phase field models at mesoscopic scale
- Mean field models for microstructural evolutions
- Thermodynamic calculations (CALPHAD model, Thermocalc) and DICTRA
- Coupled thermal , phase transformation, stress calculations (Sysweld, Zebulon), micromechanics (Abaqus…)
Members
CNRS researchers
- Imed-Eddine BENRABAH
- Maeva COTTURA
- Julien DA COSTA TEIXEIRA
- Guillaume GEANDIER
Professors, assistant professors
- Sébastien ALLAIN
- Benoit APPOLAIRE
- Lucile DEZERALD
- Vladimir ESIN
Technical and support staff
Post-doctoral researchers
- Clélia COUCHET
- Chih-Kang HUANG
- Houssam KHAROUJI
- Olha NAKONECHNA
- Arjun RAMASIMHA VARMA
- Digvijay SINGH
PhD students
- Romain BOURDAIS
- Miguel COSTA SALAZAR
- Alexy DECROOCQ
- Mohamad Ali NOUN
- Roufeida REMICHI
Emeritus
- Sabine DENIS
- Elisabeth GAUTIER
- Abdelkrim REDJAIMIA
Publications
Contact
Head of the group
Benoît APPOLAIRE
benoit.appolaire@univ-lorraine.fr
+33 (0) 3 72 74 26 91
Nancy-Artem
Institut Jean Lamour
Campus Artem
2 allée André Guinier - BP 50840
54011 NANCY Cedex