Solidification group
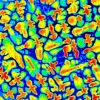
Radial section image of a directionally solidified CMSX-4 superalloy sample obtained by image analysis on a BSE contrast micrograph, revealing chemical microsegregation in a dendrite array
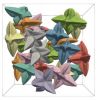
Simulation of the growth of interacting equiaxed grains (27 grains). The colours represent crystallographic orientations
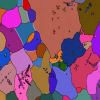
EBSD mapping of a rapidly solidified rose gold alloy showing divorced nucleation
Last publications
- Fluid-solid heat transfer analysis: In situ validation and calibration of a boiling meter using a combined experimental-numerical heat transfer approach
Abdelkabir Zaite, Himanshi Kharkwal, Hervé Combeau, Lounès Tadrist
Flow Measurement and Instrumentation, 2025, 104, pp.102905. ⟨10.1016/j.flowmeasinst.2025.102905⟩ - Simulation and analysis of small angle scattering (SAS) patterns of Ni-based superalloy microstructures generated by a phase-field model
Stéphane Berbenni, Rémi Dingreville, Thomas Schenk
Computational Materials Science, 2025, 258, pp.114086. ⟨10.1016/j.commatsci.2025.114086⟩ - Synthesis and Characterization of Metallic (Fe‐Ni, Fe‐Ni‐Si) Reference Materials for SIMS 34S/32S Measurements
Célia Dalou, Lenny Riguet, Johan Villeneuve, Laurent Tissandier, Thomas Rigaudier, Damien Cividini, Julien Zollinger, Guillaume Paris
Geostandards and Geoanalytical Research, 2024, 48 (4), pp.927-940. ⟨10.1111/ggr.12584⟩
Presentation
The Solidification group studies liquid-solid phase transformations to improve the quality of metallurgical products which are manufactured using a solidification process. Its research activity takes advantage of the close association between the study of the formation of structures and phases during solidification, and that of solidification processes. The research covers all the characteristic scales of solidification from the atomic one to the product.
One of the specific features of the group is its use of a complementary approach combining:
- The development of model experiments that make it possible to overcome the difficulty of measurement and characterization in industrial processes that are often complex,
- Skills in multiscale numerical modelling and simulation: at the scale of elementary physical mechanisms, at intermediate scales, and that of the process.
The group also develops oriented and fundamental research thanks to the elaboration of numerous solid and long-lasting relationships with industrial partners. These allow us to stay abreast of the demands for performance and quality of metallurgical products. This conception of research has enabled the group to obtain an industrial chair "Solidification" from 2020 onwards.
The Solidification group collaborates on this topic with other teams in the laboratory: Metallurgy and Surfaces; Surfaces and Interfaces, Chemical Reactivity of Materials; Process Metallurgy; Mechanics and Plasticity of Physics.
Since 2004, the group has worked in the framework of contracts with the European Space Agency (ESA) conducting micro and hyper-gravity experiments. Since 2018, it has coordinated an ESA thematic team dedicated to fusion applied to additive manufacturing.
Research topics
Refinement of solidification microstructures
The first step in a phase transition is the formation of aggregates of the new phase at the atomic scale. This phenomenon is called nucleation, and it is crucial in many scientific disciplines ranging from astrophysics to biology. It is a first-order phenomenon in metallurgy for understanding of the formation of microstructures: The size and shape of grains in metals and their alloys determine performance in structural and functional applications. The aim of this topic is to use new experimental approaches to understand the mechanisms behind grain formation during solidification. The research focuses in particular on understanding the structure of the liquid phase to control grain size and final microstructure.
Project:
Industrial contract with the CTIF 2018-2021, Contrat PSPC ISA3 2020-2023
Thesis:
- CIFRE CTIF 2018-2021 Hélène QUEHEN
- PSPC ISA3 2020-2023 Victor Moudin
Articles:
- Solidification of metallic alloys: Does the structure of the liquid matter?, Metal. Mater. Trans. A 51 (2020),2651–2664.
- Influence of minor Cr additions on crystal growth in rapidly solidified Al-20Zn alloys, Materials 13(2) (2020) 379.
- Influence of Ir additions and Icosahedral Short-Range Order (ISRO) on nucleation and growth kinetics in Au-20.5wt.%Cu-4.5wt.%Ag alloy, Metal. Mater. Trans. A 50 (5) (2019), 2279 – 2288.
Dynamics of the mushy zone
In the transition zone between the solid and liquid states, the so-called mushy zone, a solid grows in the form of microstructures out of equilibrium. The dynamics of this zone depend on both the macroscopic scale transport phenomena of the process (thermal, liquid flow, transport of chemical species) and the evolution of microstructures (thermodynamics, growth kinetics, morphology). Strong couplings between all these phenomena are decisive for the evolution of the mushy zone and for the formation of heterogeneities and structural and chemical defects in the solidified structure. The first objective of this topic is to understand the mechanisms of formation of these heterogeneities. Their origins can be found, for example, in: flow instabilities, sedimentation of particles or interactions between crystalline grains during their growth. The second objective is to develop multi-scale modelling tools to simulate these phenomena and to use them as tools for further study.
Projects:
- RESEM IRT M2P MiTeXFA 2018-2020
- LabEx DAMAS 2020-2023
Thesis:
- Labex Damas / Onera 2020–2023 Abdelhalim CHIROUF
Articles:
- Mesoscopic modeling of spacing and grain selection in columnar dendritic solidification: Envelope versus phase-field model, Acta Mater. 122 (2017) 386–399.
- Packing of sedimenting equiaxed dendrites, Phys. Rev. E 97 (2018) 012910.
- Upscaling mesoscopic simulation results to develop constitutive relations for macroscopic modeling of equiaxed dendritic solidification, Materialia 5 (2019) 100231.
Solidification processes
The aim of this field is to increase knowledge concerning the mechanisms involved in the processes for the production of high tonnage metallurgical semi-finished products. The complexity of the process lies in the strong coupling between heat, mass and momentum transfers. The group works on processes for the elaboration of large ingots by continuous / semi-continuous casting. Effective mastery of these processes is essential to improve the properties of the materials. It requires an in-depth understanding of the phenomena involved during solidification: Size, grain morphology, solidification texture, chemical segregation. These are decisive factors for the downstream stages of the overall product development process. The group’s expertise lies in the characterization of these quantities on industrial products, and the development of models. The SOLID simulation software (https://www.scconsultants.com/produits/gamme-solidification.html is developed in this framework and is commercialized by the S&CC company (https://www.scconsultants.com/).
Projects:
- FUI Soft-Defis, 2016–2020
- Industrial contract with EDF, Framatome, Industeel, ArcelorMittal, 2018-2020
- OpenSolid – industrial contract with 9 partners 2019-2022
Thesis:
FUI Soft-Defis Savya SACHI
Articles:
- Predictive Capabilities of Multiphysics and Multiscale Models in Modeling Solidification of Steel Ingots and DC Casting of Aluminum, JOM, 68, 2198-2206 (2016).
- Modeling of the Coupling of Microstructure and Macrosegregation in a Direct Chill Cast Al-Cu Billet, Metall. Mater. Trans. A. 48 (2017) 4713–4734.
- Three-Dimensional Methodology to Characterize Large Dendritic Equiaxed Grains in Industrial Steel Ingots, Materials (Basel, Switzerland) (2018), 11 (6).
Joining and additive manufacturing
The group focuses on processes involving a rapid solidification process that combine high thermal gradients with solidification rates higher than one centimetre per second. Heterogeneous joining consists of joining two chemically and structurally different materials; additive manufacturing consists in building a part layer by layer with a filler metal. The common point between these two processes is the formation of microstructures from structurally or chemically heterogeneous liquid and from solids that also possess microstructural and chemical heterogeneity. This topic aims to develop the knowledge associated with the formation of microstructures from a non-homogeneous state and under extreme cooling conditions.
Projects:
- Industrial contract with the Institut de Soudure, 2019–2022
- Contract ESA MELTING 2019-2021
- Contract PSPC PAMPROD 2019–2022
Theses:
- CIFRE IS 2019-2022 Ivan CAZIC
- PSPC PAMPROD 2019-2022 Ilia USHAKOV
Articles:
- Interface microstructure formation in Fe / Fe-Mn-C steel RSW joints, J. Mater. Process. Tech. 252 (2018) 697 – 704.
- New insights into the origin of fine equiaxed microstructures in additively manufactured Inconel 718, Scripta Mater. 195 (2021) 113740.
- Microstructure evolution of diffusion welded 304L/Zircaloy4 with copper interlayer, Mater. Des. 116 (2017) 386-394.
Industrial Chair “Solidification”
During continuous casting or large ingots castings of steel, a phenomenon of chemical segregation occurs, which can have consequences on subsequent manufacturing processes. In particular, modeling these segregation phenomena will be of primary focus in order to better anticipate them and optimize the subsequent processing stages.
Know-how
Processing
- Cold crucible induction melting furnace for the synthesis of alloys
- Bridgman directional solidification and quenching furnaces for controlled solidification conditions
- Free-falling droplet experiment for 1D solidification under extreme conditions of temperature gradients and solidification rates
- Transparent models and model materials for the in-situ study of phenomena coupling transport and growth
Modelling
- CrystalFoam, 3D software for the simulation of grain growth at the mesoscopic scale
- GGDEM (General Geometry Discrete Element Method), 3D "in house" software for the study of grain packing at the mesoscopic scale
- SOLID®, 2D software, and OpenSOLID, 3D software, for the prediction of phases, solidification structures and macrosegregations
Members
CNRS researchers
Professors, assistant professors
- Hervé COMBEAU
- Dominique DALOZ
- Julien ZOLLINGER
Tenure tracks
- Jacob KENNEDY
Post-doctoral researchers
- Chih-Kang HUANG
- Mehdi MEDJKOUNE
- Eduardo REVERTE PALOMINO
PhD students
- Ifzal HUSSAIN
- Aymeric RAKOTO
- Alan Michel VAISSIERE
Publications
Contact
Head of the group
Julien ZOLLINGER
julien.zollinger@univ-lorraine.fr
+33 (0) 3 72 74 26 69
Nancy-Artem
Institut Jean Lamour
Campus Artem
2 allée André Guinier - BP 50840
54011 NANCY Cedex