Materials and Additive Processes group
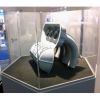
Air intake manifold for motor racing printed by selective laser sintering of polymer/quasicrystal composite powders. PAQc® materials are marketed by CINI SA.
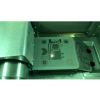
View of direct imprinting of metal parts by laser fusion on a powder-bed of aluminium alloy.
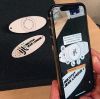
3D/4D Printing - integration of new, improved or evolving functional properties in time or space. The example shows the IJL 3D logo, integrating unique anti-copying and anti-counterfeiting materials in the format of a 3D Bleam Code (interaction with the object in enhanced reality).
Last publications
- Essai préliminaire de l'application de l'impression 3D à la modélisation physique des massifs rocheux
Jana Jaber, Marianne Conin, Olivier Deck, Olivier Godard, Samuel Kenzari
Revue française de Géotechnique, 2021, 168, pp.1. ⟨10.1051/geotech/2021011⟩ - Investigation of the Mechanical Behavior of 3D Printed Polyamide-12 Joints for Reduced Scale Models of Rock Mass
Jana Jaber, Marianne Conin, Olivier Deck, Mohamed Moumni, Olivier Godard, Samuel Kenzari
Rock Mechanics and Rock Engineering, 2020, 53 (6), pp.2687-2705. ⟨10.1007/s00603-020-02064-9⟩ - Architectural effect on 3D elastic properties and anisotropy of cubic lattice structures
Paul Lohmuller, Julien Favre, Samuel Kenzari, Boris Piotrowski, Laurent Peltier, Pascal Laheurte
Materials & Design, 2019, 182, pp.108059. ⟨10.1016/j.matdes.2019.108059⟩
Presentation
The Materials and Additive Processes’ technological research group (ERT MPA) functions as a mapping team that provides an interface between laboratory concerns and the socio-economic world. Its work combines basic research on materials in the laboratory and R&D on processes, with a view to large-scale production.
The group is interested in the development of materials adapted to additive technologies to lead to new functional materials such as bulk complex materials or those used as reinforcements in composites. Experimental development is associated with an inherent concern for innovation which facilitates technology transfer to application sectors.
Its activity is based on the additive development of new metallic, ceramic, polymer and composite materials. The additive techniques used or developed specifically for the targeted application sectors (aeronautics, automotive, space, medical), are based on the shaping of a sample object, layer by layer (by fusion, sintering, spreading, deposition, etc.). The final sample corresponds to the successive stacking of each layer. The samples can then be studied by following a characterization path adapted for each project (X-ray diffraction, electron microscopy, tribological, mechanical studies, etc.), to understand the evolution of their functional properties (volume or surface) and to optimize the material-process coupling.
The group collaborates with other IJL research groups : Metallurgy and Surfaces; Spintronics and Nanomagnetism; Chemistry and Electrochemistry of Materials; Physics, Mechanics and Plasticity; Micro and Nanosystems; Bio-Sourced Materials.
It also collaborates with many teams from national laboratories and some industrial companies:
- BBFil
- CHRU Nancy
- CINI SA
- CIRTES
- EMSE - Ecole des Mines de Saint-Etienne
- ERPI - Equipe de Recherche sur les Processus Innovatifs
- GeoRessources - Laboratoire de recherche en géologie
- ICMCB - Institut de Chimie de la Matière Condensée de Bordeaux
- ICMR - Institut de Chimie Moléculaire de Reims
- ICPEES - Institut de chimie et procédés pour l’énergie
- l’environnement et la santé, ICS - Institut Charles Sadron
- INRIA / LORIA - laboratoire lorrain de recherche en informatique et ses applications
- INSERM - BioMatériaux & BioIngénierie
- IRR - Institut Régional de Réadaptation - Nancy - Louis-Pierquin
- IS2M - Institut de Science des Matériaux de Mulhouse
- LEM3 - Laboratoire d'étude des microstructures et de mécanique des matériaux
- LIMSI - Laboratoire d'Informatique pour la Mécanique et les Sciences de l'Ingénieur
- LISM - Laboratoire d'Ingénierie et Sciences des Matériaux
- LRGP - Laboratoire Réactions et Génie des Procédés (UMR 7274)
- MIPS - Modélisation, Intelligence, Processus et Systèmes
- UBleam
Research topics
Polymer-based materials for 3D / 4D printing
3D/4D printing of materials evolving over time (or in space) is a theme that is extremely promising in terms of technological innovation. For several years now, the group has been developing this 3D/4D printing activity in collaboration with numerous academic and industrial players. The objectives are to obtain magneto-active, photo-active and electro-active objects that can be directly integrated into the 3D manufacturing of functional 4D devices.
The group is part of an important regional dynamic in the East of France to develop materials adapted to the technological needs of the future.
Projects:
- MIPPI 4D, FRCR Far East Region, 2019-2022
- ORTHOSIS 4D, LUE ANR, 2019-2021
- MAGNETO 4D, pre-mat CNRS, 2018-2020
- 4DP, Inter-Carnot MICA-ICEEL, 2018-2021
- PHOTO 3D, Carnot ICEEL, 2020-2022
- STONE3D, Carnot ICEEL, 2018-2020
- P-Tronics, SATT Paris Saclay, 2016-2018
Patent:
- Manufacture of piezoelectric components and devices using a three-dimensional printing process, PCT/EP2019/078567.
Metal-based materials for 3D / 4D printing
The lines of research developed relate to the additive manufacture of new metallic, composite or meso-structured materials. The group is also interested in the development of porous materials with 3D architecture, optimized for post-treatment of metallic or polymer infiltration. The final objective is to create modular materials, i.e. materials with physical or geometrical characteristics that evolve over time and/or with gradients of functional properties. This is an exploratory field, where many locks exist, both metallurgically and in terms of shaping.
Project:
- MIMOSA, ANR LabEX DAMAS, 2016-2019
Thesis:
- MIMOSA - Mesostructured Materials and Metallic Infiltration with Architectural Skeleton Optimization, Paul LOHMULLER, Defended 29/11/2019, University of Lorraine, Metz
Articles:
- Architectural effect on 3D elastic properties and anisotropy of cubic lattice structures, P. Lohmuller et al., Materials & Design 182, 108059, 2019.
- Stress concentration and mechanical strength of cubic lattice architectures, P. Lohmuller et al., Materials 11(7), 1146, 2018.
- A continuous crystallographic approach to generate cubic lattices and its effect on relative stiffness of architecture materials, J. Favre et al., Additive Manufacturing 21, 359-368, 2018.
Anti-counterfeiting materials for 2D or 3D printing etc.
Additive technologies and the entire upstream digital chain are today able to reproduce components very precisely in their shape and finish. This opens a new door to counterfeiting through increasingly accessible equipment. Beyond the economic impact and the degradation of the brand image of companies, the lack of control over the physico-chemical properties of the materials used in counterfeiting can lead to non-conformities and security flaws with potentially serious consequences.
The materials developed by the group can be integrated into the tools to combat counterfeiting by Strong Authentication. These materials can be adapted and shaped by all polymer technologies. They contain unique crystallographic signatures that cannot be deciphered after their development. Thus, each material can be used as a unique imprint in a given object. Finally, the use of these materials can also be considered in all application sectors that are victims of counterfeiting.
Project:
- SAM, SATT SAYENS, 2017-2019, in the process of transfer.
Patents:
- Anti-counterfeiting object, deposit n° FR1908174
- Method of authenticating an object, Europe n° EP3428628.
Know-how
Development of additive / 3D - 4D printing
- 3D printing: SLS (Selective Laser Sintering), SLM (Selective Laser Melting), FDM (Fused Deposition Modelling), Additive deposits of materials (liquids, gels, putty)
- 4D printing: shaping of objects made of multi-materials with reversible and/or evolutionary properties
Characterization
- Determination of mechanical properties (tension/compression, DMA), tribological properties (wear, friction), phases and microstructures (DRX, SEM, ATD)
Intellectual Property and Technology Transfer
- Scientific/technological monitoring related to additive materials and processes, prior study, anticipation of innovative projects
- Coordination and protection of research work in close relationship with development services (CNRS, University of Lorraine) and intellectual/industrial property firms
- Analysis of patentability search reports, adjustment of projects / studies
- Transfer to application sectors, adaptation of the materials developed to the change of scale.
Members
Technical and support staff
- Olivier GODARD
- Samuel KENZARI
- Paul LOHMULLER
Publications
Contact
Group leader
Samuel KENZARI
samuel.kenzari@univ-lorraine.fr
Tél. : + 33 (0)3 72 74 27 11
Nancy-Artem
Institut Jean Lamour
Campus Artem
2 allée André Guinier - BP 50840
54011 NANCY Cedex